How to improve the efficiency of your warehouse
- Written by News Company
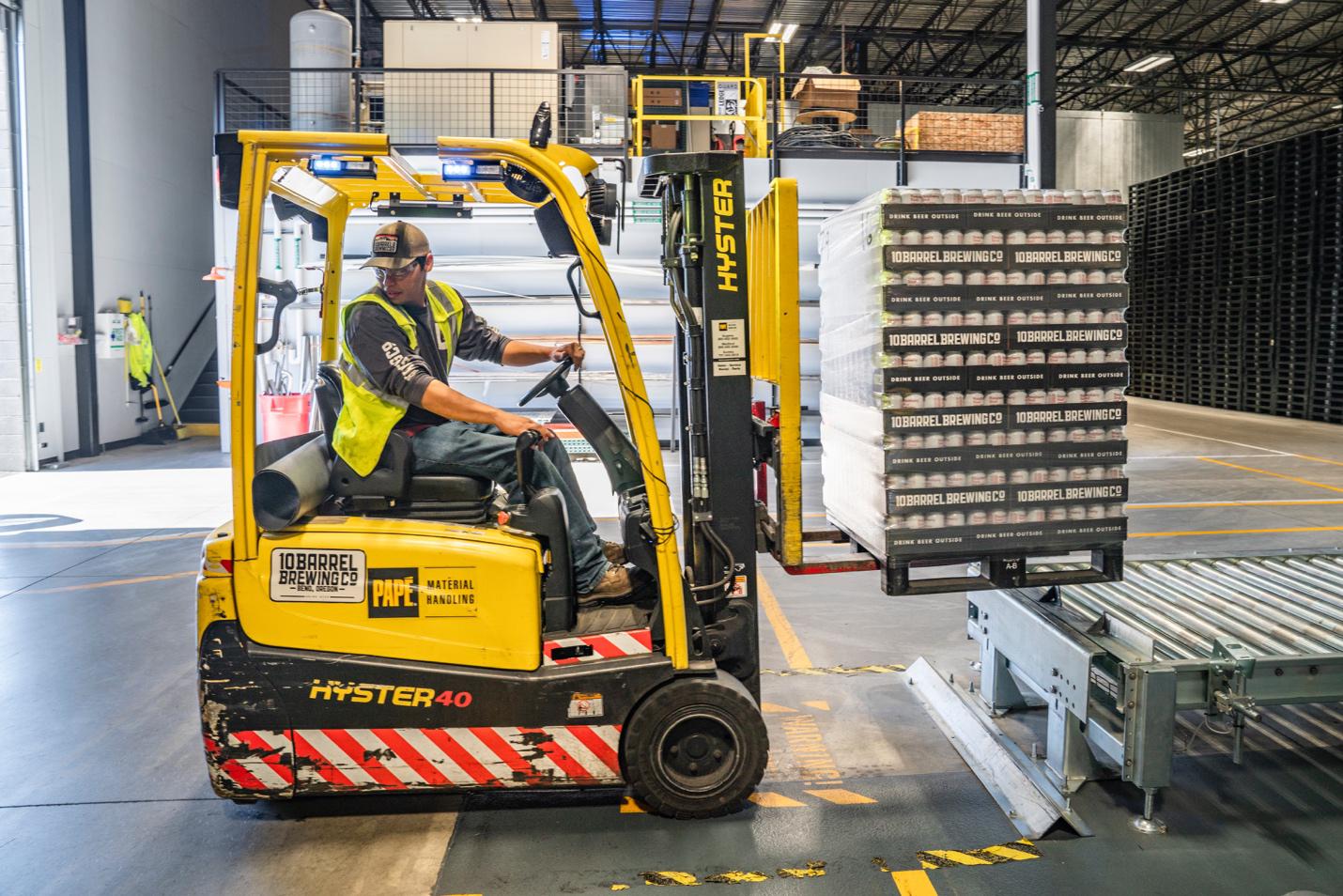
Running a warehouse-based business can be extremely challenging, but when your warehouse is running efficiently, it can offer cost savings and give you an edge over your competition. There are several factors that go into running your warehouse efficiently, which we have listed below:
Use the right forklifts
Increasing business demands and advancements in technology have resulted in the creation of a huge array of different forklift designs. With a variety of forklifts for hire available on the market, it can be tricky to choose the right option for your warehouse. Non fuelled type forklifts are a great option as they do not require diesel or petrol in order to operate and are extremely cost-effective. However, you would need to have gas available onsite when the vehicle needs to be refuelled. Diesel operated forklifts are a more economical upfront purchase and can be fuelled up quickly, but the cost of diesel can be quite expensive over a long period of time. Electric forklifts are an eco-friendly option as they do not give off any harmful emissions. This also makes them ideal for indoor use.
Optimise and maximise the available space
Instead of expanding your warehouse's footprint, it's a good idea to consider how you can make the most of its entire space. Before looking at expanding the size of your premises or adding new building fixtures to your current operations, always look to ensure you have maximised the full use of your current warehouse facility. Using pallet racks to store smaller items, for example, is a huge waste of space and can make it more likely that you will lose items. Rather than using the same shelving system throughout your entire warehouse, it's better to consider having a more advanced pallet racking solution in order to store various products.
Organise workstations
Setting up established workstations can have a huge impact on the productivity and efficiency of your warehouse operations, as staff do not have to take time out of their day to rummage around searching for the right equipment and tools. In order to make sure that your workstations are as organised as they can be, experts advise warehouse managers to use the 5S methodology seen in lean manufacturing. The five 'S's are 'sustain, standardise, sort, set in order and shine', which are designed to minimise clutter, improve organisation and safety and reduce errors.
Optimise labour efficiency
If your warehouse management system is not able to produce optimised picking plans, you can generate them manually. Take a look at your patterns of material usage and store the highest-volume items close to the front of the building in order to cut down on travel time. It's also a good idea to store goods that are often sold together close to each other. If you make the effort to keep the most regularly used items in the most accessible locations, you can reduce picking delays and streamline your warehouse operations.
Adopt appropriate technology
An enterprise resource planning system with a robust WMS (warehouse management system) module or a warehouse management system itself can optimise your operations by recommending the best techniques for picking items and putting them away. The right system will also provide you with automated pick lists that can be transferred to devices and mobile readers in order to reduce wasted paper and time and eliminate errors. Your warehouse will not only be more organised, but it will be more environmentally friendly too! Using radio frequency identification or barcode readers can make transactions more accurate and reduce picking errors.
A final point to consider is don’t overstock your warehouse and only keep what you need. Analyse the different sections of the warehouse to see what stock can be minimised and trimmed down to only have what you require.
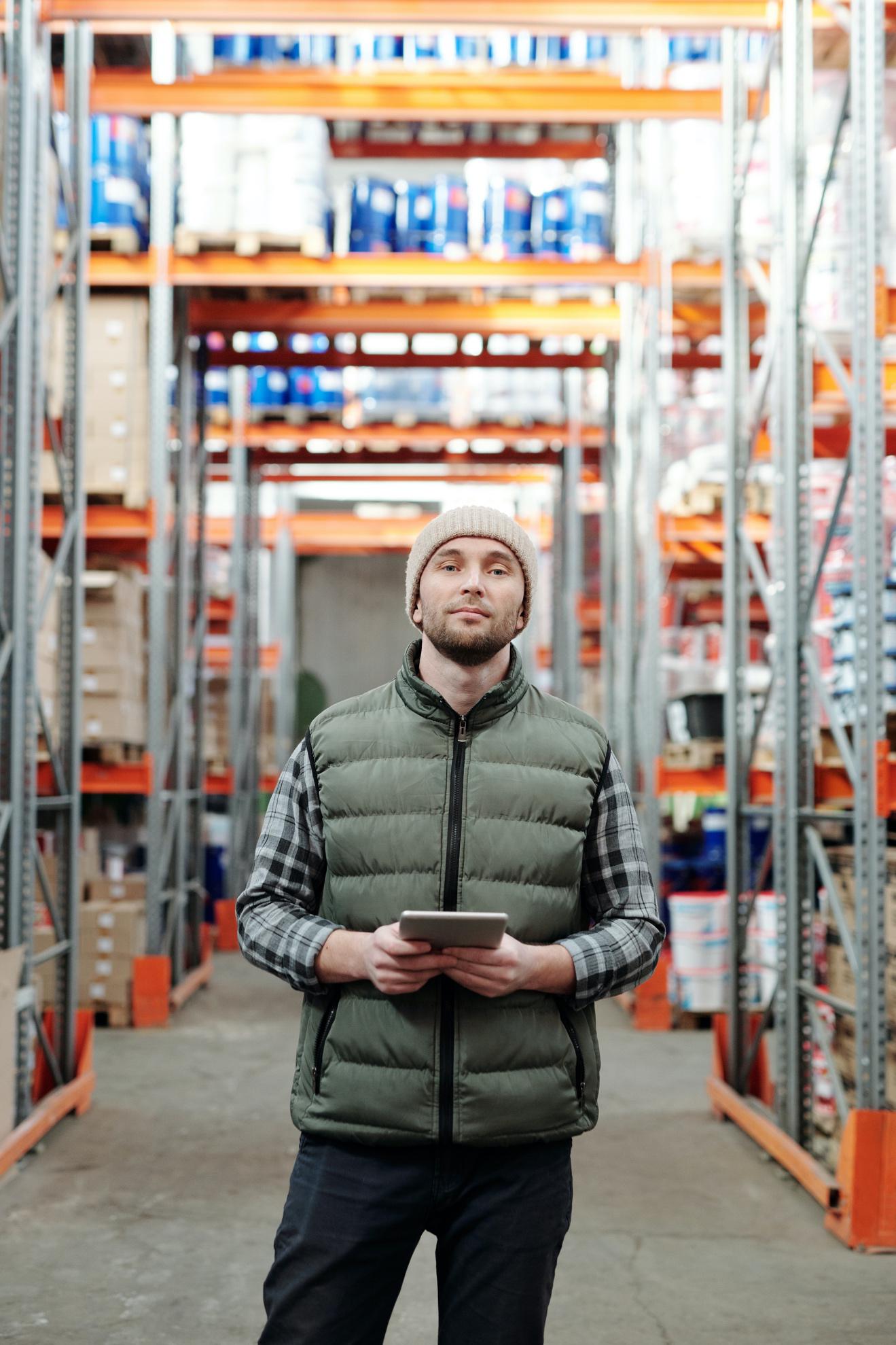